Water utilities worldwide are under increasing pressure to deliver more with less. Ageing infrastructure, growing demand, environmental challenges, and regulatory compliance all demand smarter, more efficient operations. Yet many of the most critical water assets, including pipelines, reservoirs, pumping stations, and metering points, are located in remote or rural areas where conventional cellular connectivity is either unreliable or unavailable.
This connectivity gap has long been a barrier to digital transformation in the water sector. Without reliable communication between remote assets and central systems, utilities face costly manual inspections, delayed responses, and fragmented data. Satellite IoT is helping to bridge that divide, bringing off-grid infrastructure online and enabling smarter, more efficient operations. While proprietary satellite IoT has served this role for decades, a newer, standards-based alternative is now emerging: NTN NB-IoT (Non-Terrestrial Network Narrowband Internet of Things).
NTN NB-IoT, part of the 3GPP standard for satellite-enabled IoT communications, allows connected sensors to communicate with satellites using the same NB-IoT protocol, and chipset, that they would use to connect to a terrestrial network. Economies of scale means that this drives down the cost of the chipset, delivering lower hardware costs, and potentially lower airtime costs too. For water utilities, this unlocks applications that might have been cost-prohibitive prior to the advent of standards-based satellite IoT.
At Ground Control, we specialize in enabling satellite-based connectivity and telemetry solutions for critical infrastructure. As NTN NB-IoT technology matures, we’re perfectly positioned to help water utilities leverage it to extend smart monitoring and control to the very edges of their networks. Here’s how NTN NB-IoT differs from proprietary satellite IoT and where it adds value to smarter water utility operations.
Rethinking Remote Connectivity
As water utilities continue to extend monitoring and automation efforts in remote and rural environments, satellite communication has been, and remains, critical to bridge connectivity gaps where cellular networks are unreliable or unavailable. Until very recently, the only option for utilizing satellites was to use a proprietary satellite module, e.g. if you wanted to utilize the Iridium satellite constellation, you would need an Iridium module.
These proprietary solutions are are built for purpose; the designers have not had to limit their modules’ capabilities to the 3GPP standard, which of course started as a cellular standard. This means you can send more data, more quickly, through a proprietary solution.
Further, if you’re using a message-based proprietary solution, such as Iridium’s Short Burst Data service, Iridium Messaging Transport (IMT), or Viasat IoT Nano, you also get the benefit of power efficiency.
Proprietary solutions, therefore, have been a trusted option for many years, providing reliable, low bandwidth satellite communication for mission critical data such as flow rates, tank levels, pump status, and alarm notifications. They have proven particularly valuable for applications requiring near real-time data or coverage in truly isolated areas.
However, when it comes to massive IoT deployments, proprietary solutions have limitations. Relatively high device and airtime costs, and proprietary integration requirements can make services like SBD, IMT and IoT Nano challenging to deploy at scale, particularly for low-power sensor networks or distributed metering systems.
Enter NTN NB-IoT (what is NTN NB-IoT?).
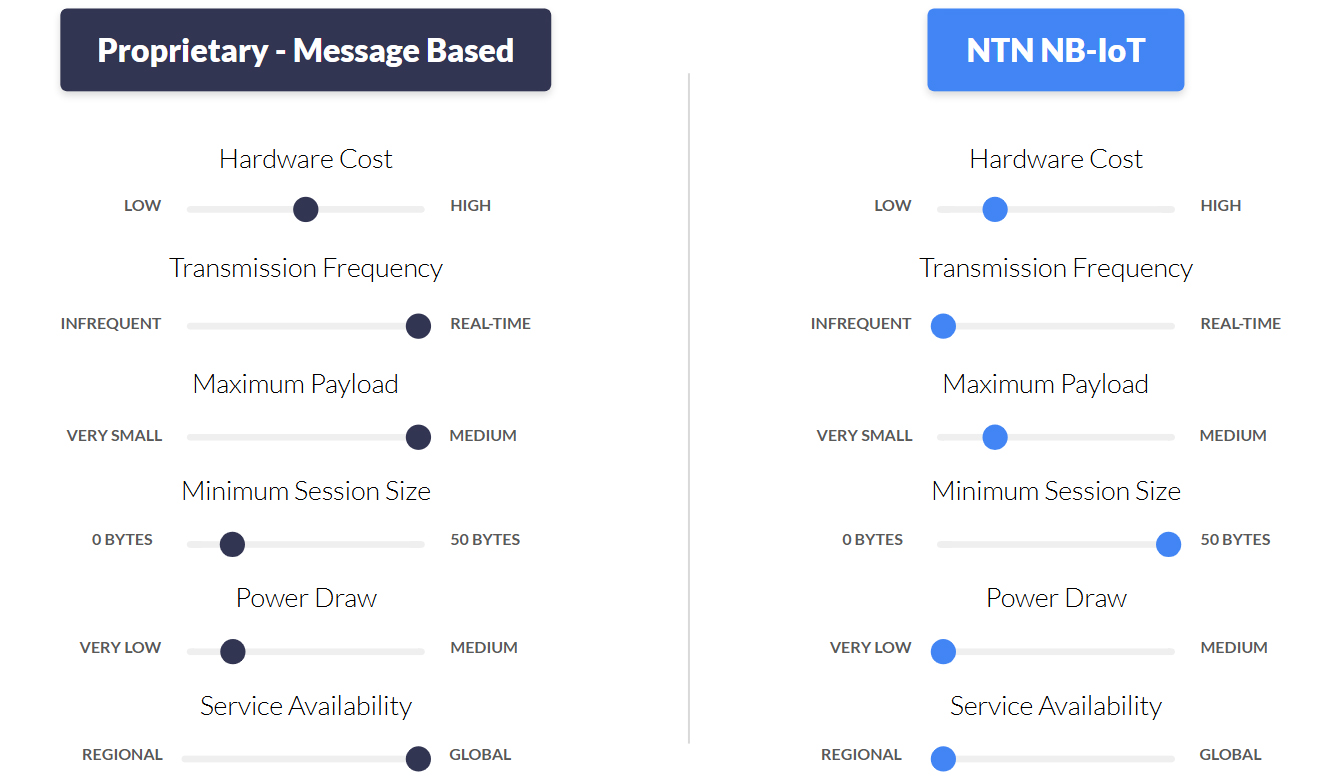
For water utilities, NTN NB-IoT could be a breakthrough. Water utility providers can deploy NTN NB-IoT-enabled sensors, meters, and monitoring equipment in places that were previously cost-prohibitive to connect via proprietary satellite IoT.
What are the Applications for NTN NB-IoT in Water Utilities?
For a water utility weighing NTN NB‑IoT against higher‑bandwidth proprietary satellite links, the sweet spot is infrequent, small payload telemetry where truly global reach (no cell towers) matters more than millisecond alerts. Typical deployments include:
Daily or multi‑hour meter reads
Remote or off‑grid customer meters (flow, volume) that only need to report once or twice a day for billing or usage analysis. A 200 byte payload can easily carry several readings, supporting rural homes, farms, or remote industrial sites.
Tank level and reservoir monitoring
Track water levels, detect overflow risks and monitor usage trends in storage facilities far from population centers. Gravity‑fed storage tanks in remote service areas report level and temperature every few hours – enough to plan refills without real‑time urgency.
Environmental baseline sensing
pH, turbidity, conductivity or chlorine residual sensors on remote intakes or treatment sites. These can trickle in (no pun intended!) once per shift or per day to track long term trends, enabling insight into water quality, and supporting regulatory compliance.
Pump run‑hours and basic status
Hourly or daily “I’m alive” heartbeats plus simple ON/OFF or run‑time counters to track remote booster stations or solar powered pumps, helping to reduce downtime and extend the life of critical infrastructure.
Pipeline integrity logs
Low frequency pressure, flow rate and structural vibration snapshots in isolated, hard to access terrain, allowing early detection of leaks, bursts or blockages to reduce water loss.
Asset inventory and location
Periodic GPS pings and motion/tamper alerts from mobile test vans, valve exercise robots or floating sensors in open canals, optimizing maintenance schedules and improving operational security.
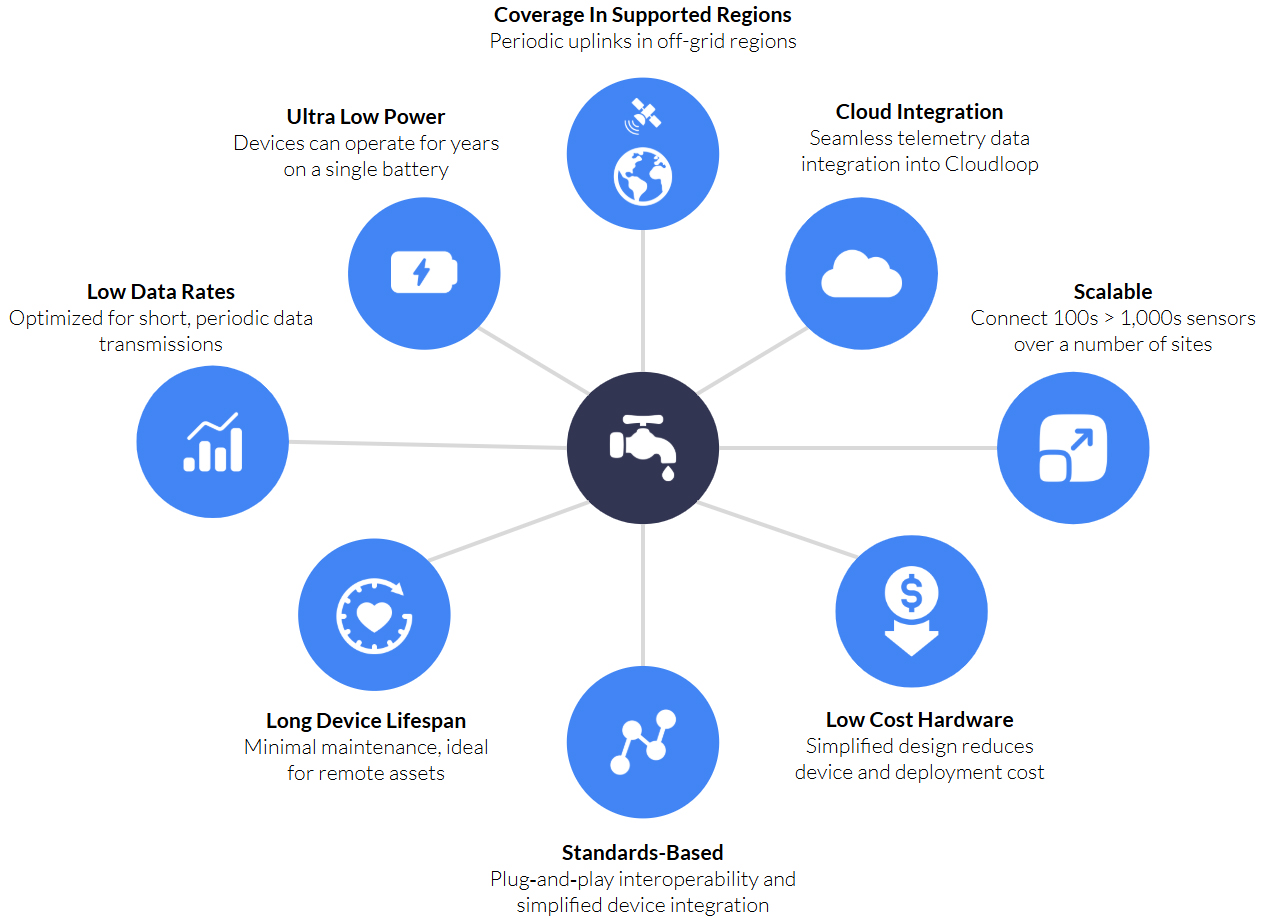
Beyond NTN NB‑IoT: Scenarios Requiring Real Time Satellite Links
Here are the water‑utility applications that really demand real time links and higher data volumes – i.e. where you’d reach for a proprietary satellite IoT service such as SBD, IMT or IoT Nano, rather than NTN NB‑IoT:
Instant leak/failure alerts
Continuous pressure or flow monitoring that must trigger sub‑minute alarms when a burst or major leak occurs.
Remote valve actuation and control
Two‑way commands (open/close, throttling) with confirmation feedback to isolate sections of pipe or adjust flow on demand.
SCADA‑style telemetry
High frequency readings (e.g. every few seconds or minutes) from multiple sensors (pressure, temperature, vibration) at booster stations and treatment plants.
Video or acoustic inspection
Transmitting snapshots, short video clips or high‑resolution acoustic signatures from remote intake structures or pipeline inspection robots.
Predictive maintenance analytics
Bulk uploads of rich sensor datasets (e.g. vibration spectra, pump performance curves) to cloud analytics for failure prediction.
Bi‑directional firmware updates and diagnostics
Pushing larger firmware or configuration payloads OTA (over the air), plus logging back detailed health / status reports in real time.
Event‑driven sampling
Millisecond‑resolution burst data (e.g. transient pressure spikes) that need to be streamed offsite immediately for analysis.
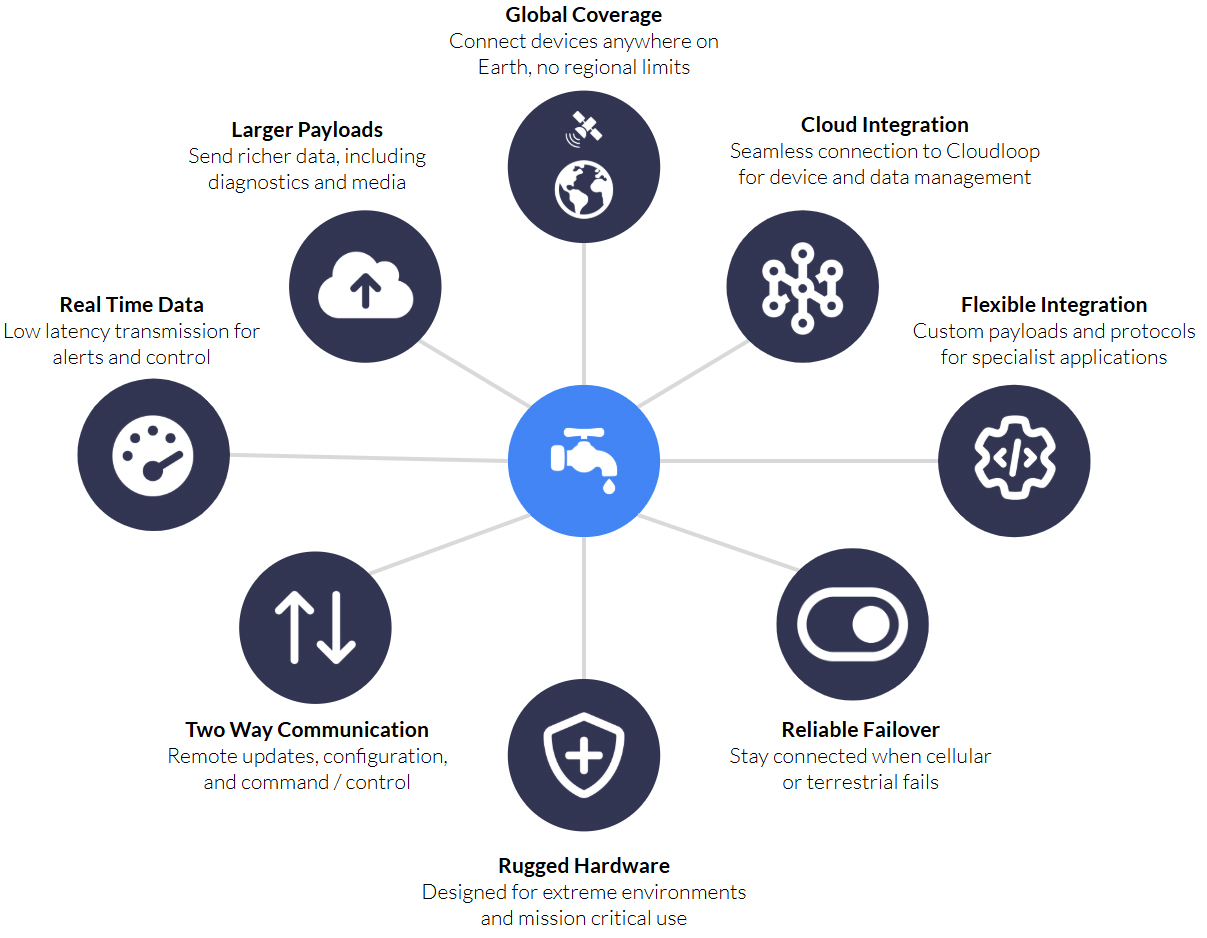
Emergency backup SCADA link
A full‑bandwidth failover channel when terrestrial SCADA lines go down, to keep control room visibility alive.
These use cases all hinge on low latency, two way communication and/or bulk data transfers; capabilities that proprietary satellite IoT is designed to deliver.
What is NTN NB-IoT?
Simply, NTN NB-IoT allows data to travel over satellite using the same standard as terrestrial NB-IoT. This means that the same chipset can be used for satellite or cellular connectivity, leading to lower hardware costs, and potentially, lower airtime costs.
It doesn’t, however, mean that it is identical to terrestrial NB-IoT, and network architects need to bear its limitations in mind. We’ve outlined some of the key differences in the following table:
NTN NB-IoT (via Skylo) |
Cellular NB-IoT |
Proprietary Satellite IoT |
|
Max Practical Payload |
256 bytes |
1,400 - 1,600 bytes |
100,000 bytes |
Latency |
High (10 - 60 s); MVNO scheduling ⟶ 2 - 5 min |
Low (1 - 10 seconds) |
Medium (c. 10 seconds) |
Directionality |
Bidirectional (protocol level) but uplink-focused in practice |
Bidirectional |
Bidirectional |
Coverage |
United States, Canada, Brazil, Australia, New Zealand and select European markets |
Terrestrial (nationwide but no maritime/remote) |
Global |
Typical Transmissions Per Day |
Common MVNO plans: ~1 - 3 uplinks/day (entry tiers) |
No strict cap: supports thousands to tens of thousands of uplinks/day (limited only by data plan allowances) |
No strict cap; governed by data plan allowances |
In summary, users can anticipate smaller data volumes, and intermittent data transmission (e.g. a few times per day), allowing devices to operate for years on battery and solar power. NTN NB-IoT is, therefore, ideal for low bandwidth, low power, and long life IoT applications.
A Smarter Approach to Connectivity
NTN NB‑IoT shines when you need occasional, small payload uplinks from truly off-grid assets. Its standards based 3GPP Release 17 stack makes integration straightforward, devices run for years on battery, and you can monitor things like daily meter reads, tank levels, water‑quality snapshots or pump “heartbeats” in remote terrain without laying any infrastructure.
Proprietary satellite IoT earns its keep when you need low latency, high volume, two way links, for real time leak/failure alarms, remote valve control, SCADA‑style bursts, video or acoustic inspections, large OTA updates, and emergency failover.
With decades of experience in satellite communications, Ground Control offers more than just connectivity; we deliver complete, integrated solutions from device to cloud. So, whether you’re starting a pilot water management project or scaling a nationwide deployment, we’re here to help you harness the full potential of NTN NB-IoT and build a smarter, more resilient, and efficient water utility network.
Ready to explore your options?
Curious which satellite technology is right for your application? Whether you’re rolling out smart meters in rural areas or need real time alerts from critical infrastructure, we can help you choose the best fit solution.
Talk to our team for a side-by-side comparison of NTN NB-IoT and proprietary satellite IoT, based on your data needs, latency requirements, and power constraints.
Email hello@groundcontrol.com or complete the form, and we’ll be in touch within one working day.