Heavy industrial sectors have continued to push the boundaries of what is possible in some of the most remote and challenging locations on the planet. Industry 4.0 has been a transformative technological leap for the traditional industries of mining, agriculture, forestry and construction, bringing new monitoring and automation capabilities to the heavy equipment that these sectors rely on.
In remote mining, farming, forestry or construction sites, an equipment breakdown can cost thousands in downtime. For industries operating far from cellular coverage, ensuring machinery stays operational is a challenge that Satellite IoT is solving with real-time data and monitoring. In this blog, we’ll explore how IoT can enable the transformation of heavy machinery operations, tackling issues like maximizing cost of ownership, preventing downtime, and safety and environmental compliance.
Heavy Equipment Total Cost of Ownership (TCO)
Purchasing specialized heavy equipment is a significant investment, and in recent years those costs have been steadily climbing as manufacturers pass on their increased raw material and labor costs. The Capital Expenditure (CapEx) involved means that each machine must be operated effectively, efficiently and within agreed tolerance limits to reduce maintenance costs and prevent costly downtime.
The theft of heavy equipment is also commonplace, with over 11,000 incidents of construction theft reported annually in the US and an average average loss of $35,000 to $45,000 per machine. Theft also has a considerable impact on operational timescales, as well as increased costs to replace or lease equipment.
Hazardous Work Environments
With heavy industry recognised as one of the most hazardous places to work (accounting for 63 per cent of all fatal occupational injuries) worksite safety requirements have, quite rightly, been improving on a global scale as Governments enforce a duty of care on industry operators.
However, it remains that despite these improvements, a diminishing workforce is entering these physically challenging industries based in remote locations. This has led to increased Operational Expenditure (OpEx) to attract high quality skilled candidates.
Environmental and Sustainability Targets
Heavy industry accounts for around a third of global energy consumption and emits a quarter of global Greenhouse Gas emissions. Pressures from Governments to hold businesses to account for their carbon emissions and environmental impacts particularly affect these industries.
To meet agreed environmental commitments, operations may need to invest in technology to analyse the worksite’s impact on the surrounding area and consider upgrading heavy machinery to meet emissions targets.
Operational Complexity
Keeping to contractual timescales on any large project involving heavy machinery is ultimately reliant on the equipment being reliable. Delays in specialist heavy equipment arriving on-site and unexpected breakdowns can lead to extensive project delays and wasted resources, all of which lead to an increased OpEx.
Without clearly-defined logistical operation data to coordinate fuel deliveries and material transport, an entire site could come to a standstill.
Connectivity Limitations
Mining, forestry, farming and construction operations often take place in remote locations with limited or no mobile or cable internet coverage. The cost of connecting fixed or cellular telco equipment or laying cables for site connectivity is often very expensive, especially when real-time communication is required for equipment operations or emergency protocols.
The return on investment for installing a dedicated network on a site which may only be operational for 10-15 years is often poor and can become a negative cost.
Six Innovations in Heavy Machinery Operations
Many of the issues facing industries using heavy machinery can be mitigated against by using technology, data and connectivity.
With satellite connectivity more reliable than cellular in remote locations and increasingly more competitively priced, the cost-effectiveness and profitability of mining, forestry, construction and agriculture operations can be significantly improved and many of the key issues facing the industry can be resolved.
1. Predictive Maintenance
Predictive maintenance is a data-driven approach to keeping heavy machinery operating at peak performance and efficiency. By continuously monitoring on-board sensors for feedback on tire wear, oil and fuel consumption, engine temperatures, hydraulic pressures, vibrations, stability and acceleration, machinery can be proactively inspected and maintained according to usage, rather than reactively when a breakdown occurs.
Satellite IoT devices can transmit real time data on machine usage and even enable a shutdown of equipment if thresholds are exceeded. By planning machine maintenance downtime, preventing failures that could lead to accidents, and monitoring machinery operatives driving behaviour, the operation expenditure of the site can be effectively managed and optimized.
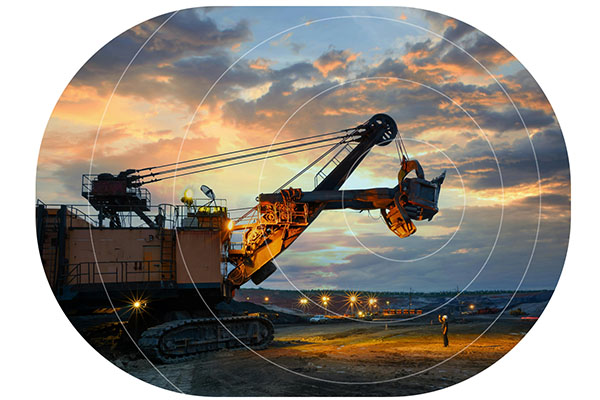
The 2021 McKinsey & Company ‘The Internet of Things’ Report highlighted that in the construction sector, employing IoT applications can improve uptime by 30 to 50 percent and increase throughput by 1 to 5 percent.
An additional benefit of monitoring machinery usage is to provide a better return on the CapEx of the machinery when the equipment is sold at the end of the project.
2. Remote Monitoring
Remote monitoring of site personnel and equipment can enable the operational efficiency of worksites, as well as ensure the safety of all workers on-site. With satellite-connected asset trackers on equipment and team members, remote operations centres can use geo-fencing capabilities to keep personnel and heavy machinery apart using safety zone alerts. Should a team member stray into the path of an oncoming vehicle, both the individual and the driver can be alerted to the potential risk.
Satellite IoT enabled sensors can detect worksite ambient conditions to ensure staff and machinery are not exposed to extreme working temperatures, strong winds, excessive rainfall or poor air quality. By encouraging and demonstrating a commitment to site safety, labor recruitment can be improved.
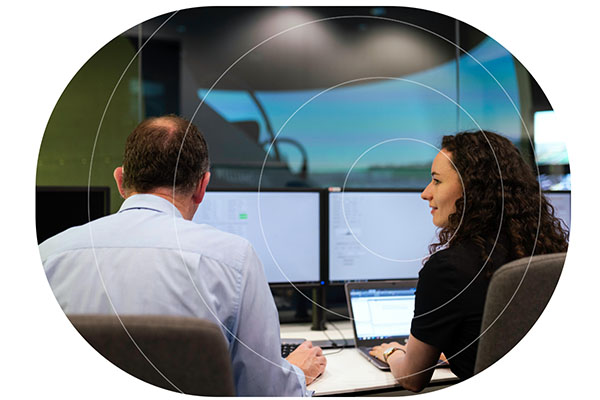
Site operations can be further optimized through monitoring of raw material tanks and silos (e.g. concrete and chemical reagents), machinery fuel consumption, generator fuel levels and final product storage and collection (e.g. metal ores, timber, grain). By integrating satellite IoT sensors across the work site, logistics managers can ensure fuel and raw material deliveries and product collections are planned according to site requirements, reducing bottlenecks and improving operational efficiency.
According to McKinsey and Company, operators which have more than 50% of their vehicle fleet connected to the internet have 23% better financial performance than peers with less than 50% connected. Companies with more than 75% of their fleet connected have 51% better financial performance.
3. Telematics
Monitoring heavy equipment on-site is integral to operational performance, and can also ensure the worksite is remaining committed to its safety, sustainability and environmental goals.
Aside from monitoring onboard sensors for predictive and reactive maintenance, telematics can also improve driver behavior, which in turn can reduce fuel consumption and carbon emissions. Heavy industry equipment by its nature burns fossil fuels and emits greenhouse gases during operation, but there are opportunities to limit these effects.
In the construction industry alone, machinery idle time averages 36% which increases fuel consumption by up to 5%. The biggest operational opportunity for reducing the potential for idling is ensuring vehicles are dispatched to their collection or drop-off locations according to requirements rather than on a continuous cycle, thereby preventing fleet waiting times.
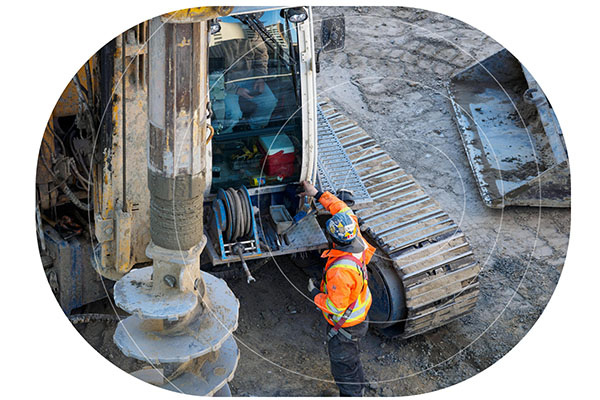
There is also driver behavior to consider, with some operators leaving machinery idling during their break periods. Using real-time telematics, Site Managers can address the machinery operator actions immediately and encourage them to turn the machine off when not in use.
Through these two simple actions it is possible to reduce fuel costs, decrease carbon emissions, limit noise pollution and improve worksite air quality. When industry profit margins are challenging, evidence has shown that operators who lag behind their peers in reducing downtime are losing future business, wasting time and money, and increasing their ecological impact on the environment.
4. Theft Prevention
Heavy equipment theft costs the USA construction and agricultural industry an estimated $300 million to $1 billion annually, and is especially prevalent during the National Holidays of Labor Day, Memorial Day, Independence Day and Thanksgiving when worksites are closed and machinery is left unattended.
Satellite-connected video surveillance can enable real-time monitoring and recording of remote worksites and storage areas to protect both staff and equipment from unauthorized access.
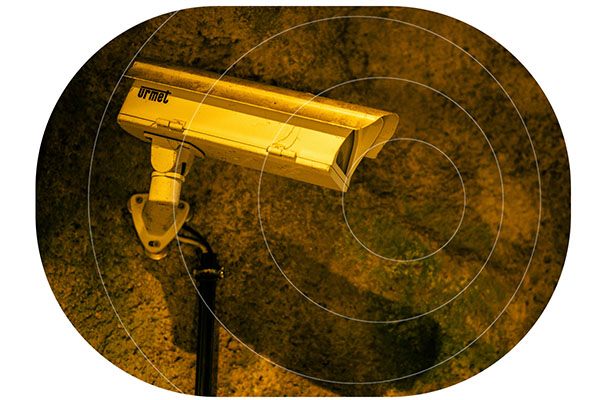
Heavy equipment can be fitted with discreet satellite asset trackers which can alert the operations team when equipment has moved out of a geofenced area or the machinery is being operated outside of normal worksite hours. Satellite assets trackers are especially effective at tracking stolen heavy machinery as they can keep connected across borders, and in the case of the Iridium network anywhere on Earth. Improvement in asset tracking capabilities has led to an increase in machinery recovery rates from 5% to 20% in the last 15 years.
5. Machine Learning and AI
Incorporating AI and machine learning capabilities into the mining, forestry, agriculture and construction industry has the potential to transform how these sectors address the challenges of CapEx and OpEx, as well as their environmental impacts. By leveraging data-driven analysis, businesses can optimize workforce and heavy machinery productivity, identify opportunities for fuel savings and emission reduction, limit raw material wastage and improve final product quality and volumes. Insights from these analyses can be replicated across multiple work site locations and integrated into cost projections for future projects, driving efficiency and sustainability.
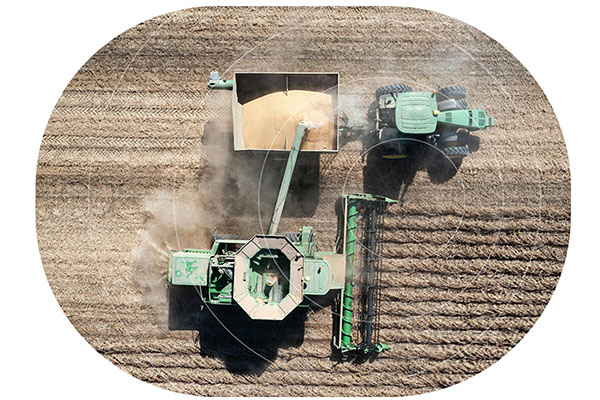
Heavy equipment can be fitted with discreet satellite asset trackers which can alert the operations team when equipment has moved out of a geofenced area or the machinery is being operated outside of normal worksite hours. Satellite assets trackers are especially effective at tracking stolen heavy machinery as they can keep connected across borders, and in the case of the Iridium network anywhere on Earth. Improvement in asset tracking capabilities has led to an increase in machinery recovery rates from 5% to 20% in the last 15 years.
6. Autonomous and Remote Control Heavy Machinery
One of the most significant challenges facing the mining, agriculture, construction, and forestry industries is an aging workforce, with many skilled workers nearing retirement and fewer new recruits stepping into these roles. Technological advancements in developing and implementing autonomous and remote operation of heavy equipment are helping to manage labor shortages while enhancing productivity and safety.
Autonomous Haulage Systems (AHS) are already in use across large-scale mining operations, enabling unmanned dump trucks to optimize hauling cycles, improve payload accuracy, and increase operational efficiency. However, not all scenarios are suitable for full automation, which is where remote control solutions come into play.
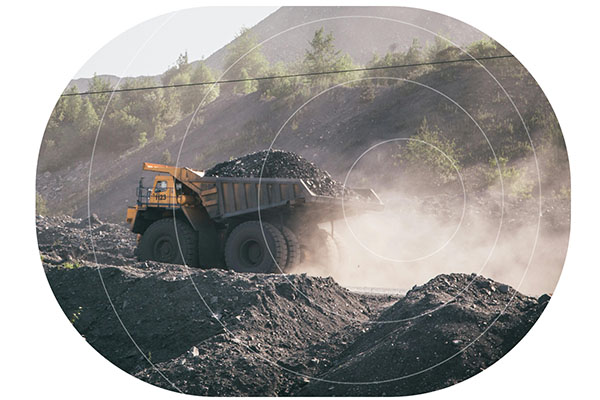
In hazardous environmental conditions or working on difficult or sloping terrain, controlling heavy machinery via remote control allows operators to manage equipment from a safe distance nearby or within a central operations hub. This minimizes risks to personnel while maintaining operational efficiency.
Both autonomous and remote-controlled systems rely on a continuous flow of real-time data, including video feeds and telemetry data, to ensure precise operation and avoid collisions. Satellite connectivity provides reliable and seamless data exchanges in remote locations, enabling the integration of automation and remote operation of heavy machinery in complex environments.
Satellite IoT Solutions for Heavy Machinery Monitoring
Satellite IoT is supporting innovation within the heavy machinery industry, addressing critical challenges such as remote connectivity, safety, and operational efficiency. By leveraging real-time data through predictive maintenance, telematics and remote monitoring, businesses can reduce costs, improve productivity, and meet stringent environmental goals. As automation and AI continue to transform the sector, embracing satellite-enabled solutions is essential for staying competitive in an increasingly connected world.
Get in Touch
Contact us to discover how our satellite IoT solutions can drive efficiency and profitability for your heavy machinery fleet.
With 20 years of experience, we can help you make the best choices based on your requirements.
Please call us on us on +44 (0) 1452 751940 (Europe, Asia, Africa, Oceania) or +1.805.783.4600 (North and South America); email hello@groundcontrol.com, or complete the form.